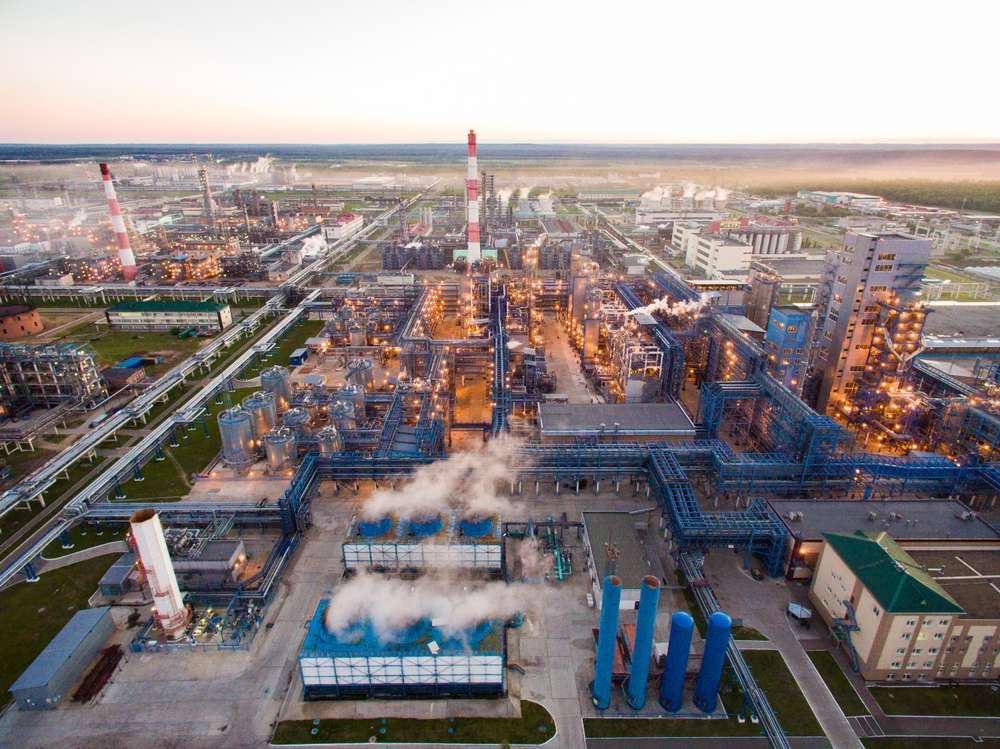
O avanço tecnológico e o desenvolvimento de pesquisas científicas permitiram o incremento de técnicas, equipamentos elétricos e inovação de processos de produção na área industrial.
Desse modo, diversos equipamentos elétricos foram incorporados aos trabalhos, além de técnicas de automação na indústria, que permitiram a minimização de erros e o significativo aumento da produtividade.
Sendo assim, a tecnologia foi uma das principais responsáveis pela criação de mecanismos de automação, isto é, que visam melhorar os produtos e, ao mesmo tempo, reduzir custos de produção.
Mas, não somente a indústria foi beneficiada, também outros segmentos como a construção civil, aeronáutica, siderúrgica, setor primário e terciário tiveram a implantação de máquinas e equipamentos automatizados, que resultou em uma ampliação dos métodos produtivos, gerando competitividade e movimentando a economia de forma positiva.
Alguns equipamentos elétricos automatizados da indústria
1. Placas de circuito impresso
Um dos equipamentos automatizadas mais usados no segmento industrial é a linha de montagem de placas de circuito impresso.
Esses componentes são essenciais no funcionamento de aparelhos e máquinas eletrônicas, portanto, é vista em diversos estabelecimentos que operam com tecnologia.
Podendo ter variações de modelo, a linha de montagem das placas de circuito impresso geralmente operam com dois métodos: o SMT (Surface Mount Technology) e o PTH (Pin Trough Hole).
Independentemente do funcionamento, essas placas são essenciais para garantir a eficiência de produção e para reduzir custos em larga escala.
2. Detector de gases
Além da questão da produtividade, a tecnologia também foi responsável por aumentar a segurança de empregados e empregadores, reduzindo as ocorrências de acidentes no local de trabalho. Por esse motivo, há vários equipamentos destinados à proteção e prevenção de riscos, como é o caso do detector de 4 gases.
Esse aparelho é especialmente voltado para identificar a presença de gases tóxicos em espaços confinados, como forma de observar os níveis e recomendar a permanência de colaboradores em determinado ambiente.
O detector de gases também pode evitar outros acidentes, como, por exemplo, explosões e incêndios que podem ser ocasionados por gases inflamáveis.
3. Controladores de potência
O controlador de fator de potência é responsável por avaliar o consumo de eletricidade, observando se há excesso de consumo reativo, o que pode indicar um problema no fator de potência.
Assim, por meio desse equipamento, é possível corrigir falhas e evitar o desperdício energético e, consequentemente, o aumento de gastos.
O fator de potência é descrito como a medida da potência elétrica consumida convertida em trabalho útil. Segundo a Agência Nacional de Energia Elétrica (ANEEL), o mínimo permitido do fator de potência é de 0,92. Ou seja, se o valor estiver abaixo disso, pode ser o indicativo de algum problema.
4. Painel elétrico de comando e de controle
O painel eletrico de comando e de controle é uma espécie de compartimento modular, usado para o armazenamento e alocação de dispositivos eletrônicos.
Em geral, esse equipamento está disponível em vários modelos, que têm objetivos diferentes. No entanto, todos trabalham com a distribuição e alimentação de fontes de energia, seja para controle de máquinas ou equipamentos, ou para a distribuição elétrica.
O centro de controle de motores (CCM), por exemplo, é um painel elétrico que contém barramentos de energia comum, com uma unidade de controle motor.
Já o quadro de distribuição, como o próprio nome já diz, tem a função de distribuição de eletricidade para pontos de consumo e outros circuitos.
Cuidados com os equipamentos elétricos da indústria
Apesar da tecnologia estar envolvida na maioria dos processos industriais, sendo ativa na automação e aprimoramento dos métodos de trabalho, é essencial manter o cuidado e atenção com equipamentos elétricos.
Isso porque o mau uso destes pode ocasionar falhas e comprometer todo o trabalho do setor, prejudicando a produtividade e, até mesmo, ocasionando eventuais acidentes.
Por esse motivo, recomenda-se a realização de ações de manutenção:
- Preventiva;
- Preditiva;
- Corretiva.
As duas primeiras formas de manutenção são feitas em caráter de prevenção, ou seja, quando o erro ainda não ocorreu, mas já são adotadas medidas para evitá-los, colaborando, assim, para aumentar a vida útil dos equipamentos.
A corretiva é feita emergencialmente, isto é, quando a falha já foi apresentada e é preciso tomar providências o quanto antes, para que o erro não prejudique a indústria e, consequentemente, a produção e os trabalhadores.